铁路的UT:车轮还是滑轨? 选择哪一个?
(在连续轨道测试中超声输入的方法–的优点和缺点)
介绍
如今,欧洲,美国,澳大利亚和其他市场(包括便携式单轨和双轨线路小车,火车头和检测车)上都有数十种连续轨道测试技术。 在大多数方法中,都采用了传统的测深方案,可以测试轨道头和轨道中央横截面:
0°–用于沿所有轨道高度的水平分层以及对声耦合的分析(按底部回波信号水平)
70°–为了检测轨头中的横向裂纹,使用了向前和向后的探头。 在搜索系统的某些修改中,使用了三个压电元件(单独使用或在一种情况下使用),从而确保对所有轨道头宽度进行测试。
35°(38°,45°)–用于对前和后探头的腹板和底座进行测深。
为了检测轨道头侧面的垂直裂纹,使用了所谓的“侧视”测深方案,其探角为40°/ 55°。
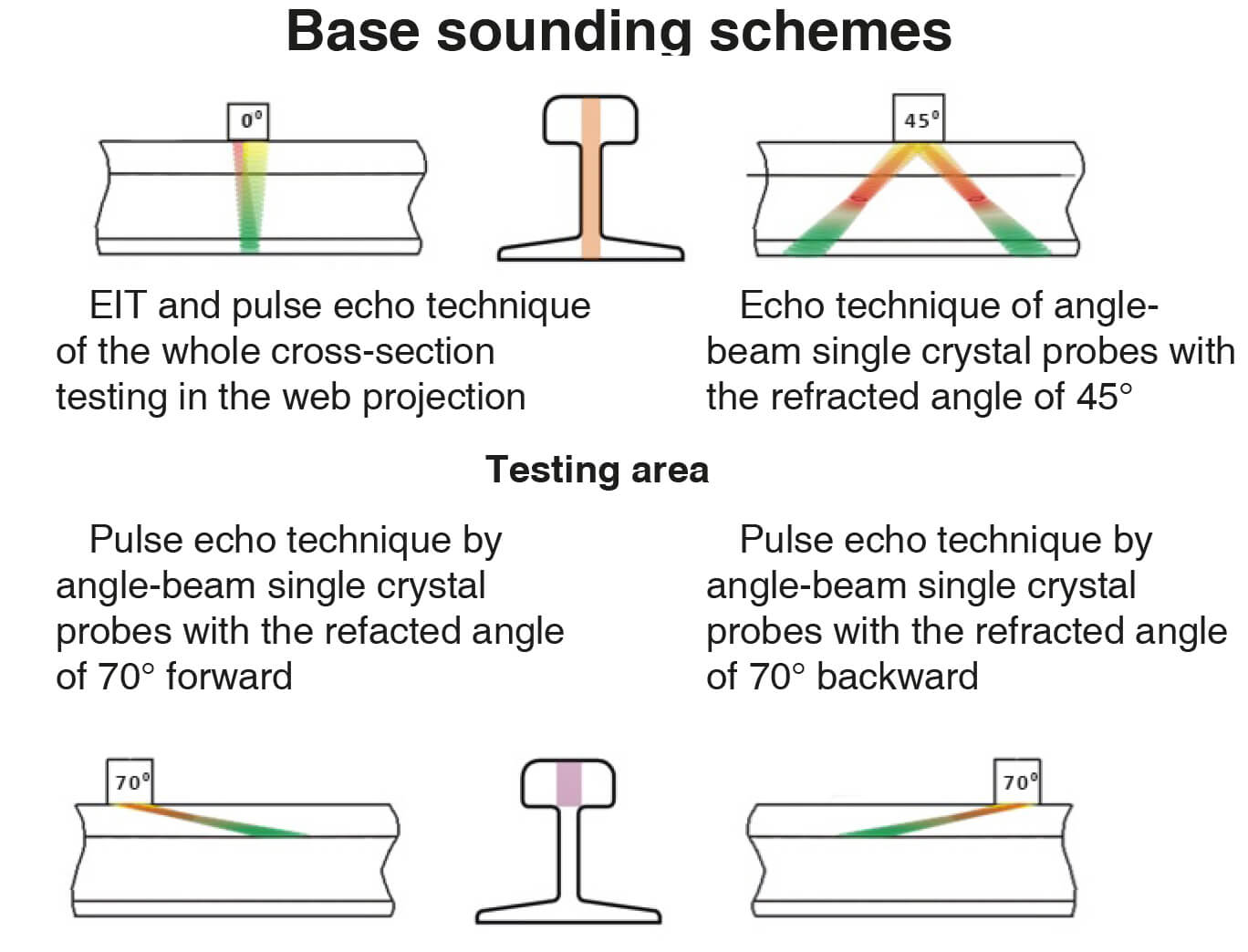
搜索系统的类型
超声波探头和超声波输入的放置主要通过两种方式进行:«超声波车轮探头»(车轮探头,参见图1)和滑动探头(«slides»),在东欧广泛使用(参见图2)。 ;
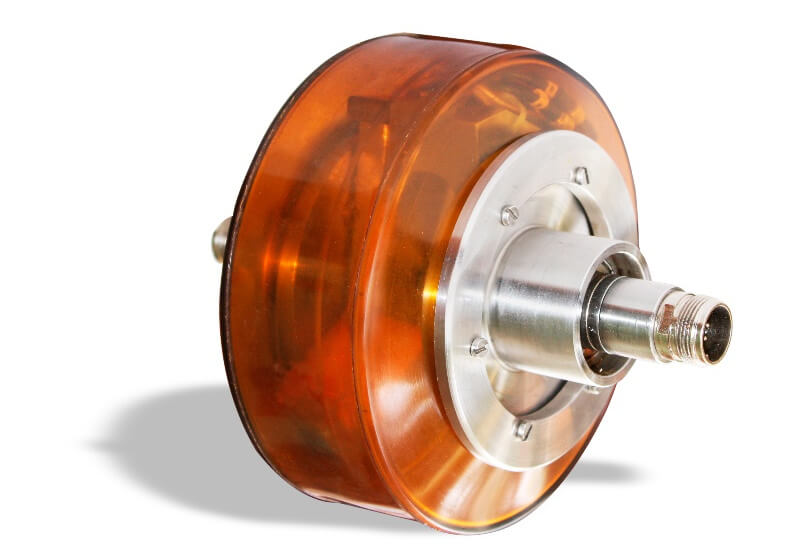
图1 –超声波轮搜索系统
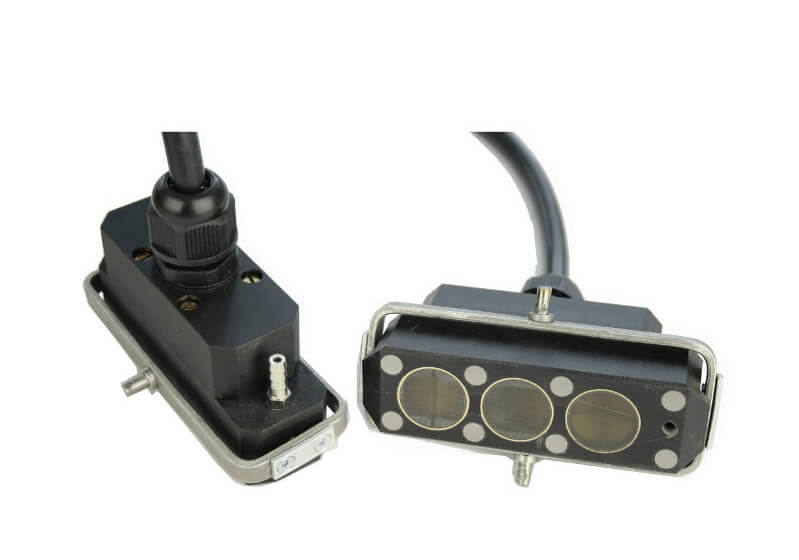
图2 –滑动搜索系统的声学单位
超声输入系统的优缺点
滑动系统
对于用于高速测试装置的滑动系统,首先,必须提供稳定的声耦合,这既可以通过自动轨道表面跟踪系统(机械部件)又可以通过 预先进行轨道浇水,并通过耦合剂系统直接喂入探针。 通过在高压(最高100 bar)下进行水喷射来浇灌和清洁导轨。
耦合剂在特定压力下供应到探头(声学单元)。 在一些非破坏性的测试设备中,耦合剂以分散的形式被喂入,这允许经济地使用它并增加声耦合的稳定性。
因此,为了确保稳定的声耦合,滑动系统需要大量消耗耦合剂(水),这是其缺点之一。
滑动系统的第二个缺点是声学单元与轨道头运行表面的直接接触,因此探针单元很快就磨损了。 为了避免探头磨损,使用了所谓的防护鞋。 防护鞋通常由有机玻璃或硬质聚氨酯制成,通常是消耗品。
UDS2-77 超声波单轨探伤仪
探索更多车轮搜索系统。
车轮搜索系统实际上是一个装有聚氨酯轮胎的车轮,内部装有超声波探头。 砂轮中充满了浸入液体(通常使用乙二醇)。 带有探头布局的车轮搜索系统如图3所示。
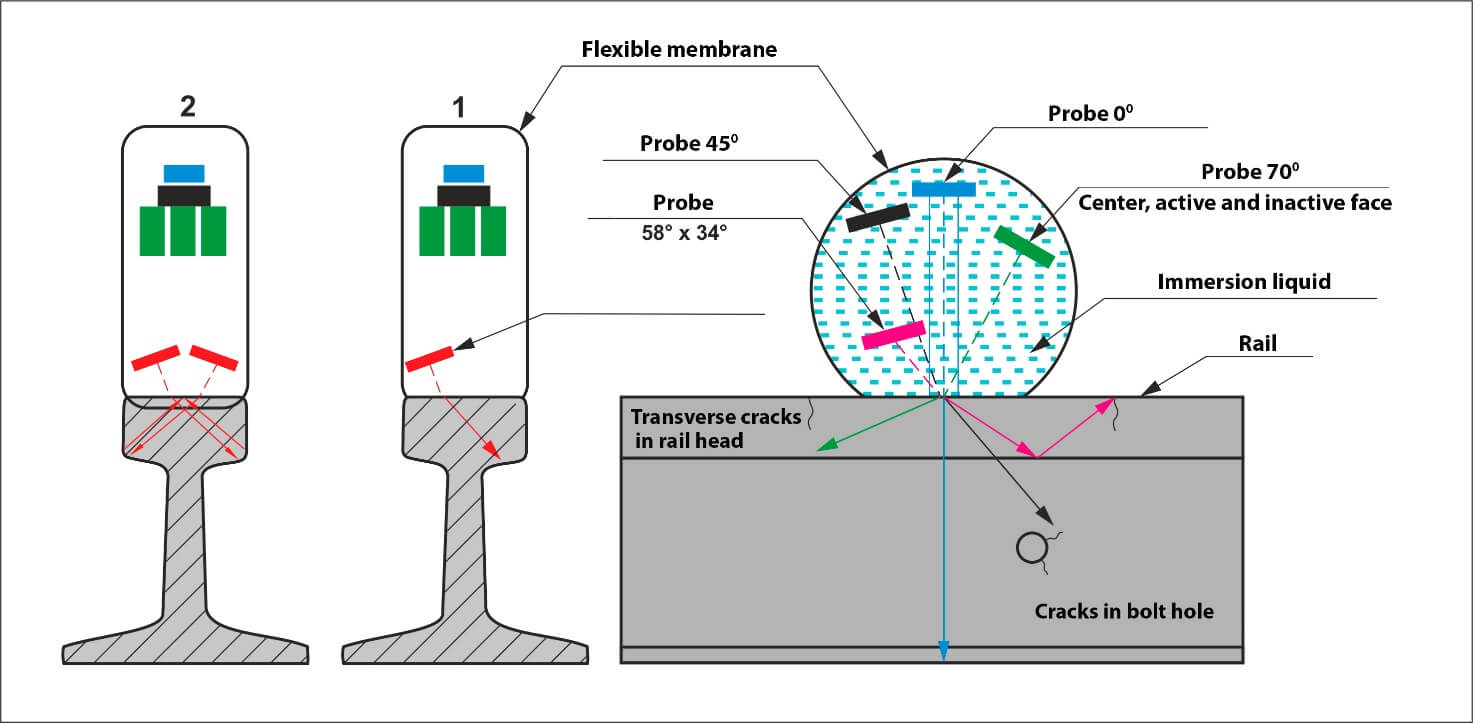
车轮搜索系统最显着的优势之一是它的弹性轮胎,即使轨道头磨损了,该轮胎也可以紧贴在轨道头行驶表面上。 而且,通过改变超声轮中的压力速率,可以调节界面点的尺寸。 这确保了声耦合的更高稳定性,进而提供了以最高40 km / h的速度测试导轨的可能性。 车轮搜索系统的另一个优势是,与滑动搜索系统相比,耦合剂的消耗量低得多。 这又通过聚氨酯轮胎得到保证。
自然,轮搜索系统具有所有优点,但也有一些缺点。 主要缺点之一是必须在所有平面中相对于轨道表面精确调整车轮位置。 在任何平面中改变10的方向都可能导致金属(在相应平面中)的探针角度改变40,并导致探测方案失真。 结果,操作员可能会错过甚至很大的缺陷。 因此,不建议在单轨探伤仪中使用车轮探针。 一些制造商忽略了此限制,而是在车轮安装在稳定杆上的情况下进行安装。 并且当其倾斜在第二导轨上时,大大降低了使用这种手推车的便利性。
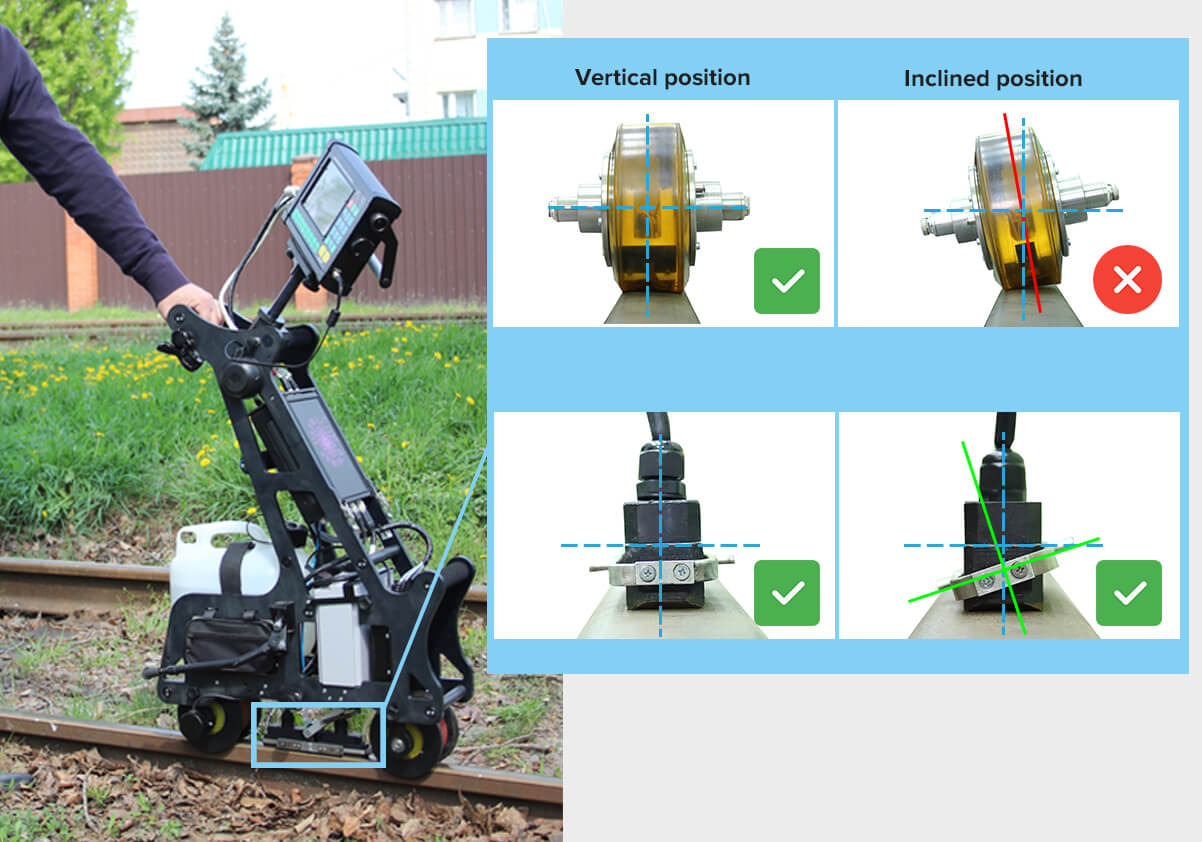
与滑动式搜索系统相比,轮式搜索系统的另一个缺点是,使用前者无法实现某些测深方案,特别是那些在探头之间需要固定距离的测深方案(例如, 串联方案)。 由于超声波轮的几何形状以及不可能和无法将它们彼此之间以所需的距离分配。 这样的缺点导致降低了轨道头中的平面内部缺陷的缺陷检测质量。
最后但并非最不重要的一点是,与测试速度限制有关的缺点是由浸入式输入法原理来限制的。 在用于超声振荡的轮系统中,从压电元件到轮辋的行进需要一些时间,该时间可以与振荡通过轨道主体的行进时间相同或者甚至更多。 结果,从发射器通过浸没液体到达导轨的底面再回到接收器所需的超声波的整个飞行时间至少是滑动系统中的两倍。 这也将限制设置回初始脉冲的频率和相应地确定必须检测到必要缺陷的扫描速度。 在使用车轮搜索系统的高速NDT装置中,扫描间距通常约为4 mm。 同时,测试速度可以达到40 km / h。
在滑动搜索系统中,超声振荡直接输入到测试对象中,并且初始脉冲的频率可以相应地增加到两倍,从而依次导致扫描速度增加或扫描间距减小 例如,在40 km / h的相同扫描速度下,滑动搜索系统中的扫描间距将等于2 mm。
结论
所描述的每种搜索系统都可以用于连续铁路称谓,每个都有其优缺点。 因此,搜索系统类型的选择主要取决于铁路服务公司的传统。 因此,ОКОndtGroup生产并不断改进搜索系统类型,幻灯片和滚轮。